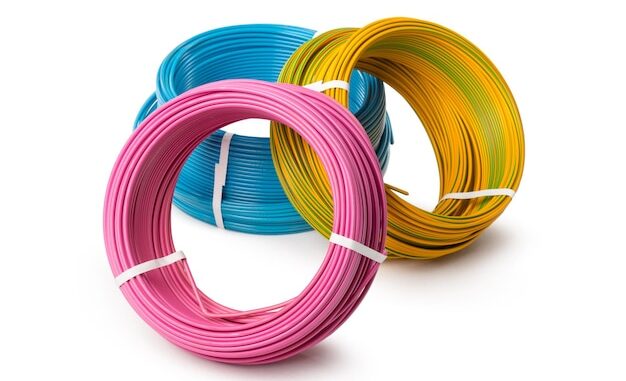
Selecting the appropriate welding wire is crucial for the success of your projects, as it can make all the difference. Flux-cored wire and solid wire are the two types of welding wire most frequently used in MIG (metal inert gas) welding. They are suitable for diverse tasks since they each have unique features, use cases, advantages, and disadvantages. This piece aims to provide you with an understanding of flux cored and solid welding wires, their strengths, and their applications so you can make an informed choice about your welding needs.
In This Content
Flux-coated wire for welding
Rather, flux-cored wire is a hollow tube that is filled with granular flux. The flux melts during the welding process and wraps around the weld, protecting the slag and weld zone with a protective gas. Since this shielding gas essentially keeps the weld pool clean from contamination by the atmosphere, flux-core wire is a particularly common choice for outdoor welding and scenarios in which supplying a shielding gas is impractical or impossible.
Benefits of Wire with Flux Coration
- Flux-cored wire is the most portable procedure and perfect for all-position welding because it doesn’t require any additional shielding gas.
- FLUX-Core: This works best with thicker materials and applications requiring a strong welding point, but it is less suitable for use with thinner materials because it can penetrate considerably deeper into the surrounding area.
- Greater Deposition Rates: Generally speaking, flux-cored wire has a higher deposition rate than solid wire, allowing you to weld more quickly and efficiently!
- Wind resistance: The flux core’s production of a shielding gas provides improved protection against wind-induced porosity, enabling outside welding in windy conditions.
Requirements for Flux-Cored Wire
- Increased spatter: Compared to solid wire, flux-cored wire produces more spatter out of the welding gun, which could need additional cleaning time.
- Not as Pretty Welds: Compared to solid wire, the slag produced by flux-cored wire may give your weld a less appealing appearance.
- Position Constraints: Due to the fact that many flux-cored wires are made for particular positions (domains), positional welding is restricted.
Solid welding wire
Solid welding wire is a solid metal rod that needs to be shielded from the atmosphere by an external gas, most often carbon dioxide or argon. Because of its versatility and ability to produce clean, visually appealing welds, MIG welding frequently uses it.
Benefits of Solid Wire
- Clean-Looking Welds: Solid wire produces welds that are relatively free of spatter, so if aesthetics is important to you, you might want to think about using solid wire to complete the job.
- Use: Suitable for all welding situations and capable of joining a large range of metals and thicknesses.
- Perfect for Novices: Solid wire is recommended for novices as it is generally simpler to understand and operate than flux-cored wire.
The drawbacks of using solid wire
- Needs Shielding Gas: Compared to flux-cored wire, solid wire is less portable since it needs an external shielding gas supply.
- Less Wind Resistance: Solid wire is less suited for outdoor welding in windy situations because it is more vulnerable to wind-induced porosity than flux-cored wire.
Selecting the appropriate cable for your task
- Choosing Flux-Cored or Solid depends on the following variables:
- Application: Are you searching for a clean, attractive weld (solid[]) or do you need extra portability and wind resistance (flux-cored)?
- Base Metal Thickness: In order to penetrate thick materials more deeply, flux-cored wire may be necessary.
- Sort of Welding Position: Choose a wire that is appropriate for a particular position or one that can be used in all situations.
- Cost: Due to its unique properties, flux-cored wire may be more costly than solid wire.
In summary
While solid wire welding is thought to be the superior option in certain situations, flux-cored and solid wire welding have their own advantages and disadvantages. What fits your needs the best varies and is dependent upon your use case. Knowing how to use these two cables can help you choose the best choice for yourself, regardless of your preferences for mobility, wind resistance, weld quality, or appearance.
For excellent advice and an extensive selection of flux-core or solid welding wire, go to [Your Company Name] at www.udo.co.th. Get assistance from our experienced staff in locating the appropriate welding wire for your upcoming job by speaking with them.
Note: Are buying departments and welders searching for premium welding wire? Visit https://www.udo.co.th/category_product/กลุ่มลวดเชื่อม to see our extensive assortment of premium brands and types. Discover the ideal welding solution right now!