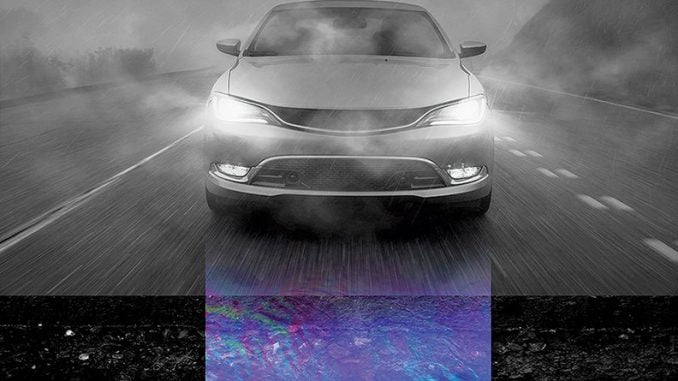
But on this day, engineers from Bosch were on the snow-covered road, testing new technology that allows automated vehicles to localize themselves — that is, figure out precisely where they are in the world — primarily via radar.
So far in the self-driving realm, automakers and technology companies have been enamored with other sensors for this purpose. Automated cars are currently using cameras and laser sensors known as lidar.
That’s changing. Whether it’s global suppliers such as Bosch, or startups such as Lunewave and WaveSense, a recent spinoff from MIT’s Lincoln Laboratory, there’s fresh innovation being wrung from radar, a technology that first found widespread use during World War II, and was first deployed on production automobiles by supplier Delphi in 1999.
With 20 million radar sensors produced for cars over the past 19 years, Bosch is no stranger to radar.
Its latest iteration is a prototype that creates a road signature, essentially a map layer that allows a vehicle to figure out its location based solely on GPS and radar information.
By coupling these two inputs, Bosch’s system can take that real-time data and compare it to its base map, match patterns between the two, and determine its location with centimeter-level accuracy.
In practice, Bosch intends for this map layer to provide redundancy to localization information that’s ordinarily obtained by cameras for both driver-assist and self-driving vehicle use. But as showcased on that snowy day along M-14, Bosch’s system can localize by radar all by itself.
The demonstration shows the car can essentially drive with its cameras blindfolded, which might be necessary if cameras are lost due to weather conditions or system glitches in the real world.
Radar, Bosch says, brings several localization advantages. It works regardless of lighting or weather conditions. Its datasets are small compared with the more rich ones created by cameras, which matters for transmitting updates of the base map layer. And it’s already in mass production; lidar is not.
The first misstep in designing sensors for automated vehicles, as Tarik Bolat sees it, is assuming that cars need to perceive their surroundings in the same way as humans.
“If we’re going to automate vehicles, we don’t simply need to convert human cognition into robot cognition,” says Bolat, CEO of WaveSense. “There are other datasets that are very useful that we can leverage that aren’t available to humans.”
The Boston-based company offers a radar system unlike any other. It uses ground-penetrating radar to essentially see through the road, and create a map of the road’s subsurface. By sending its radio waves 10 feet below the road, the system can get reflections from soil type and density, roots rocks, utility infrastructure and anything else lurking beneath the ground.
The result is a unique map that’s akin to a subterranean fingerprint. Cars can compare their position to a preloaded map and localize themselves to within 2 centimeters to 15 centimeters, depending on how fast a vehicle is traveling.
Like Bosch’s radar localization, this gives vehicles the ability to determine exactly where they are without regard for weather. In WaveSense’s case, it’s not dependent on any surface-level information, and can function regardless of whether snow or anything else is covering the road.
Born out of the Lincoln Laboratory, which develops technology for military needs, ground-penetrating radar has traditionally been used in archaeology, utility pipeline work, and search and rescue. WaveSense is believed to be the first company to use it for automotive purposes, and Bolat says the startup is working with automakers and Tier 1 suppliers to advance the radar systems toward production.
Since they were pioneered in the 1940s by German physicist Rudolf Luneburg, sphere-shaped radar antennas have captured attention for their range and 360-degree sensing capabilities. Trouble is, nobody has been able to make one small enough for practical automotive use.
Thanks to 3D printing, that’s changing. The founders of Lunewave, a startup based in Tucson, Ariz., say they’ve spent a decade perfecting the 3D printing of so-called Luneburg antennas. Roughly the size of a plum and pocked with 6,500 unique chambers, it resembles a miniature Death Star from Stars Wars.
“This is something that would have been impossible to make in a traditional manufacturing process,” Xin says.
The antenna’s unique design allows radar to sense obstacles at a distance of about 380 yards, which is nearly double what conventional units today can achieve, Xin says. Further, the sphere shape permits sensing in 360 degrees from a single unit, rather than limiting sensing to the traditional 20-degree field of view.
Lunewave’s sensor is roughly one-seventh the size of any other Luneburg antenna. By virtue of both its size and performance, it could potentially allow automakers and technology companies to reduce the number of radar sensors on a vehicle from more than half a dozen to one.
That achieves cost savings. Further, the reduction in radar units streamlines sensor-fusion processes and reduces or eliminates the need to stitch data from multiple radar units.