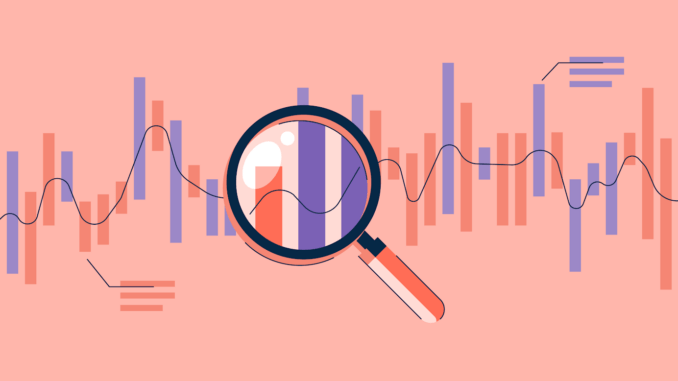
In This Content
Introduction
In the world of welding, selecting the right type of welding wire is crucial for achieving strong, high-quality welds. Two common types of welding wires are solid wire and flux-cored wire. Each type has distinct characteristics, advantages, and applications. This article provides a comparative analysis of solid wire and flux-cored wire, examining their differences, strengths, and ideal uses.
Understanding Solid Wire
Definition and Composition
Solid wire, also known as a solid MIG wire, is a type of welding wire made from a single, solid piece of metal. It is commonly used in Gas Metal Arc Welding (GMAW) or MIG (Metal Inert Gas) welding processes. Solid wires are typically made of mild steel, stainless steel, or aluminum.
Key Features
- Consistency: Provides a consistent weld with a smooth, uniform appearance.
- Strength: Offers strong welds with good mechanical properties, depending on the alloy.
- Shielding Gas: Requires an external shielding gas, such as argon or a mix of argon and CO2, to protect the weld pool from atmospheric contamination.
Advantages
- Clean Welds: Produces clean and high-quality welds with minimal spatter.
- Control: Allows for precise control of the weld bead and penetration.
- Versatility: Suitable for various applications, including thin materials and high-precision work.
Ideal Applications
- Thin Materials: Preferred for welding thin sheets of metal.
- Precision Work: Used in applications requiring precise and clean welds, such as in the automotive and aerospace industries.
Understanding Flux-Cored Wire
Definition and Composition
Flux-cored wire is a type of welding wire that contains a flux core inside a tubular metal sheath. The flux core provides additional shielding and chemical properties to enhance the welding process. Flux-cored wire can be used with or without shielding gas, depending on the type of flux-cored wire.
Key Features
- Self-Shielded vs. Gas-Shielded: Flux-cored wires come in self-shielded (no external gas required) and gas-shielded varieties.
- Flux Core: Contains a flux that creates a protective gas shield and provides additional deoxidizers and alloying elements.
Advantages
- No External Gas Needed (Self-Shielded): Self-shielded flux-cored wires do not require external shielding gas, making them suitable for outdoor or windy conditions.
- Higher Deposition Rates: Offers higher deposition rates and faster welding speeds compared to solid wires.
- Versatility in Conditions: Performs well in various positions and is less sensitive to contaminants in outdoor environments.
Ideal Applications
- Outdoor Welding: Ideal for outdoor or windy conditions where shielding gas may be blown away.
- Thicker Materials: Suitable for welding thicker materials and heavy-duty applications.
Comparative Analysis
Welding Performance
- Solid Wire: Provides a cleaner weld with less spatter and better control over the weld pool. It is ideal for applications requiring a high-quality finish.
- Flux-Cored Wire: Offers higher deposition rates and better performance in outdoor conditions. However, it may produce more spatter and require post-weld cleaning.
Cost and Efficiency
- Solid Wire: Generally, solid wire is more cost-effective in terms of material cost but requires the use of shielding gases, adding to overall expenses.
- Flux-Cored Wire: Flux-cored wire can be more economical for heavy-duty applications due to its higher deposition rate and reduced need for external shielding gas.
Versatility and Ease of Use
- Solid Wire: Best suited for indoor applications with controlled environments. It requires proper shielding gas and careful handling.
- Flux-Cored Wire: More versatile in different environments, including outdoor and less controlled conditions. It is also easier to use for thicker materials and heavy-duty tasks.
Conclusion
Both solid wire and flux-cored wire have unique advantages and applications in welding. Solid wire is preferred for its clean welds and precise control, making it ideal for thin materials and high-precision work. On the other hand, flux-cored wire offers higher deposition rates, better performance in outdoor conditions, and versatility in handling thicker materials. Understanding the characteristics and benefits of each type of welding wire can help you make an informed choice based on your specific welding needs and environmental conditions.